Mit dem neuen Verfahren der Projektions-Mikro-Stereolithografie (PµSL) eröffnet Boston Micro Fabrication (BMF)v speziell in der Mikroproduktion Alternativen zum Spritzgießen ebenso wie zur CNC-Bearbeitung – für Prototypen, aber auch Endprodukte in Serienqualität. In der additiven Fertigung mit Polymeren und Verbundwerkstoffen produzieren die microArch 3D-Drucker von BMF hochpräzise Bauteile mit 2 μm Druckauflösung und +/- 10 µm Maßstabsgenauigkeit.
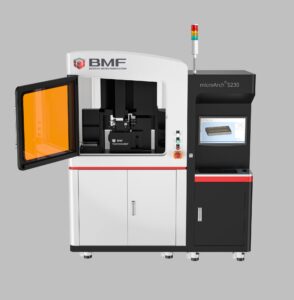
Der Trend zur Miniaturisierung von Bauteilen nimmt in allen Branchen zu. Der Bedarf an sehr kleinen, zugleich sehr komplexen Komponenten steigt in der Unterhaltungselektronik, bei medizinischen Geräten und MEMS, in den Biowissenschaften und vielen anderen Bereichen. Um fortschrittliche Funktionen und verschiedene Drahtlos-Technologien unterzubringen, werden elektronische Geräte immer dichter mit vielfältigen kleinen Komponenten bestückt. Für medizinische Anwendungen werden winzige Komponenten und sehr kleine Geräte hergestellt, die den Patienten sogar direkt implantiert werden können.
3D-Druck von BMF bietet hohe Flexibilität, geringe Stückzahlen und Kosten
Hersteller suchen nach neuen Möglichkeiten, diese kleinen, aber hochdetaillierten Produkte und Komponenten zu fertigen. Denn während die Nachfrage nach kleinen, hochpräzisen Teilen steigt, sind die herkömmlichen Fertigungsverfahren mit hohen Investitionskosten und langen Vorlaufzeiten verbunden.
Kleine Bauteile aus Kunststoff oder Polymer werden meist im kostenintensiven Mikro-Spritzgießen oder mit Hilfe der ebenso teuren Mikro-CNC-Bearbeitung gefertigt. Die Herstellung von Formen und Werkzeugen für diese winzigen Komponenten ist kostenaufwändig, weil spezielle, komplexe Werkzeuge und Vorrichtungen benötigt werden. Die hohen Vorlaufkosten im Werkzeug- und Formenbau erhöhen die Stückkosten besonders bei relativ kleinen Serien.
Deshalb bietet sich der 3D-Druck als Lösung geradezu an. Doch bisher konnten die Additiven Fertigungsmethoden die Anforderungen an Auflösung, Genauigkeit und Geschwindigkeit nicht erfüllen. Nun gibt es eine neue Technologie der additiven Fertigung, die sich preislich für viele Herstellungsszenarios anbietet. Mit Mikro-3D-Druck lassen sich hochdetaillierte Bauteile ohne kostspielen Werkzeug- und Formenbau herstellen. Weil der 3D-Druck für die Mikrofertigung wesentlich wirtschaftlicher ist als der Druck größerer Komponenten, eröffnet er kosteneffektivere Herstellungsmöglichkeiten als das Spritzgießen, mit dem zusätzlichen Vorteil einer höheren Flexibilität.
Kostenvergleich: Mikrofertigung im Spritzgießen oder im 3D-Druck
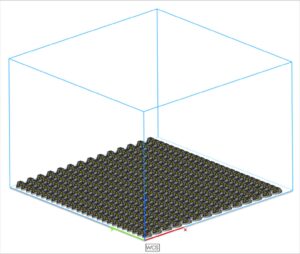
Der 3D-Druck von Bauteilen und Komponenten üblicher Größen rentiert sich bei steigenden Stückzahlen nicht mehr, sobald die geringeren Materialkosten die hohen Vorlaufkosten ausgleichen. Manche Anwendungen erreichen den Schnittpunkt bereits bei wenigen Hundert Teilen. Deshalb konnte sich 3D-Druck bisher nur bei Prototypen und relativ geringen Losgrößen durchsetzen.
Für die Mikroproduktion gelten diese Standardregeln nicht. Die Wirtschaftlichkeitsrechnung wird nahezu auf den Kopf gestellt: Einerseits verursacht der Werkzeugbau für sehr kleine Komponenten deutlich höhere Kosten. Andererseits machen die Materialkosten im 3D-Druck nur einen sehr kleinen Anteil der Herstellkosten aus, weil nur geringe Materialmengen verbraucht werden. Selbst wenn das Material für 3D-Druck das zehnfache kostet als herkömmliches Granulat, beeinflusst dies die Gesamtkosten nur wenig. Unter diesen Voraussetzungen lässt sich 3D-Druck selbst bei Stückzahlen in Zehntausenden sinnvoll für kleine, hochpräzise Bauteile einsetzen. Zwar erfordert der Einsatz additiver Fertigungstechnologie die Anschaffung eines oder mehrerer 3D-Drucker, was kostspielige Investitionen bedeuten kann. Allerdings amortisiert sich diese Anschaffung über die Zeit, und im Gegensatz zu Formen und speziellen Werkzeugen können die Drucker später ohne zusätzliche Kosten (und Formen) zur Herstellung anderer Teile verwendet werden.
Boston Micro Fabrication (BMF) kommerzialisiert ein 3D-Druck-Verfahren namens Projektions-Mikro-Stereolithografie oder PµSL. PµSL ähnelt anderen Technologien wie SLA oder DLP auf dem Markt, aber mit einigen wichtigen Unterschieden. Obwohl das Verfahren auf dem Prinzip der Stereolithografie beruht, sorgt die Technologie durch einen UV-Lichtblitz für eine schnelle Photopolymerisation einer ganzen Harzschicht in Mikro-Auflösung. Dadurch erreicht der Prozess eine ultrahohe Genauigkeit, Detailtreue und Auflösung, die mit anderen Verfahren nicht möglich sind.
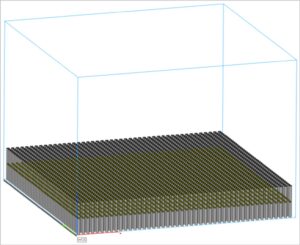
Die 3D-Drucker der microArch-Baureihe von BMF weisen eine hochpräzise Linse zwischen der Lichtquelle, einer DLP Projektion und dem Harzbad auf. Die Drucker steuern die XYZ-Bewegungen zudem sehr genau, wozu Hochpräzisionstische verwendet werden, wie sie auch in Koordinatenmessmaschinen zu finden sind. Die Kombination und Koordination dieser Systeme ermöglicht je nach System eine optische Auflösung von 2 bis 10 Mikron und erreicht damit eine enge Toleranz in dem Bereich von +/- 25 µm. In Verbindung mit der hohen Geschwindigkeit des DLP ergibt dieser Ansatz die hohen Leistungen und den Durchsatz, der für industrielle Anwendungen benötigt wird.
Die Linie der microArch 3D-Drucker von BMF umfasst drei Serien, gegliedert nach der erreichbaren Auflösung. Der P150 ist das Einsteigermodell der Mikropräzisions-3D-Druckerserie von BMF. Mit einer Auflösung bis zu 25 µm und geringeren Investitionskosten eignet er sich perfekt für kleine, detailreiche Teile, die keine ultrahohe Auflösung erfordern. Die zweite Serie umfasst Drucker mit einer hohen Auflösung bis 10 µm und einem großen Bauraum für industrielle Anwendungen.
Die höchste Auflösung bis zu 2 µm bietet die Druckerserie, der das neue Spitzenmodell microArch S230 angehört. Der microArch S230 bietet Forschungslaboren und Herstellern, die Mikroteile mit engen Toleranzen als Prototypen oder Serienteile benötigen, eine nie dagewesene Designfreiheit und Detailauflösung. Er ermöglicht ein Bauvolumen von 50 x 50 x 50 Millimetern und bis zu fünfmal schnelleres Drucken als die Vorgängermodelle der 2μm-Serie. Zu den weiteren Hauptmerkmalen des microArch S230 gehören aktive Schichtnivellierung, automatische Laserkalibrierung und die Fähigkeit, Materialien mit höherem Molekulargewicht und einer Viskosität von bis zu 20.000 Cp zu verarbeiten, was die Herstellung von stärkeren Funktionsteilen ermöglicht.
Offenes Materialsystem für Flüssigpolymere in microArch-Druckern
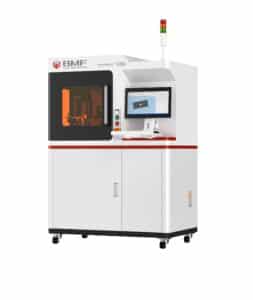
BMF bietet zu allen Druckern ein offenes Materialsystem an. Anwender können mit speziell definierten Flüssigpolymeren von BMF ebenso arbeiten wie mit anderen Materialen ihrer Wahl. Die BMF-Linie von Photopolymeren umfasst harte, steife hochtemperaturbeständige, biokompatible und haltbare Materiale für funktionale Endverbrauchsteile. Gerade wurde das Materialangebot erweitert:
- AL (Aluminiumoxid) Keramik – Ein biokompatibles und chemikalienbeständiges keramisches Harz für Anwendungen mit hohen Temperaturen, großer Festigkeit und hoher Steifigkeit, wie im Werkzeugbau (Spritzguss), bei Gehäusen und medizinische Geräten.
- HT 200 – Ein haltbares, hochtemperaturbeständiges und hochfestes Harz, das gelötet werden kann und für die Endanwendung bei elektrischen Steckverbindern und elektrischen Komponenten vorgesehen ist.
- MT (Magnesiumtitanat)-Keramik – Die Kombination aus hoher Dielektrizitätskonstante und geringem dielektrischen Verlust macht MT-Keramik geeignet für Millimeterwellenanwendungen wie Antennen, Wellenleiter und andere elektronische Komponenten.
Mikropräziser 3D-Druck öffnet einen kosteneffektiven Weg, um die Herausforderungen der Miniaturisierung in vielen Branchen zu meistern. Ohne die hohen Kosten spezieller Formen und Werkzeuge bringt dieser Weg eine hohe Flexibilität für die Produktion. Bei Anwendungen im Mikrobereich, die in der Elektronik, Medizintechnik und anderen Branchen immer häufiger werden, führt die Möglichkeit zum 3D-Druck von Hunderten oder Tausenden von Teilen zu echten wirtschaftlichen Einsparungen, besseren Reaktionsfähigkeiten auf Änderungen von Produktdesign oder Marktbedingungen. Wegen der Vorteile des Mikropräzisions-3D-Drucks lassen sich bei industrieüblichen Serien geringere Kosten erreichen als mit Spritzgießen oder Mikro-CNC-Bearbeitung.